There are many individuals and organizations involved in Formula 1 who would like to be thought of as "Movers and shakers", but few deserve this title more than Servotest Ltd. , based in Feltham, Middlesex, England.
There are many individuals and organizations involved in Formula 1 who would like to be thought of as "Movers and shakers", but few deserve this title more than Servotest Ltd. , based in Feltham, Middlesex, England. As suppliers of servo hydraulic test and motion simulation systems to most Formula 1 teams and much of the rest of motor racing, Servotest designs and builds the equipment that is used to both test components to destruction and to simulate running conditions off-track, in the laboratory. Their motor racing business is currently a little less than 10% of their total business, but with ever greater restrictions on track testing in all formulae, they are experiencing an increased level of interest in their products as teams gear up to perform more and more of the routine durability proving and basic setting-up back at the factory.
Any engineering system, whether it be a structure or a mechanism, is either subject to loads applied to it, which result in displacements, or parts are constrained to move, which results in loads building up within it. For many years in motor racing these loads and displacements could only be estimated by calculation and applied statically, using weights and hydraulic cylinders to simulate certain discrete conditions experienced during running. The arrival of data logging systems in the late 1960s and early 70s allowed engineers to accumulate time histories of loads and displacements experienced while the car was driven at racing speeds on the track. Once the PC enabled engineers to handle all this data in an efficient manner, it did not take long before they wanted to use it to drive force/displacement actuators to simulate track conditions dynamically in their labs, so that they could both test for durability and be able to watch and analyze the performance of their structures and mechanisms.
 |
|
 |
It is the dynamic requirements, whether they involve random motion, chassis and suspension frequency oscillations of under 30cycles/second, or tire, engine, and transmission vibrations at frequencies up to 500Hz, that set the performance standards of the simulation system. Maintaining precisely varying loads as the application points of those loads move at velocities of several meters/second, sets the specifications for the actuators, the control system, and the hydraulic power supply to drive the system. Power requirements for hydraulic test rigs may be several hundred KW in the case of car test systems. This level of expertise in the design, engineering and build of custom systems is best found in a specialist company, rather than developed in-house. Servotest, with its staff of 50, more than 75% of whom are engineers, has built up that expertise over more than 40 years. It is therefore not surprising that so many Formula 1 teams have turned to them for their biggest test equipment investment after wind tunnels - the 7-post rig - as well as other, less glamorous test systems.
 |
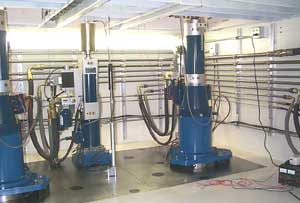 |
Fig 3 - View of wheel actuators and aeroloader actuator (center) |
© Servotest Ltd. |
|
 |
The 7-post rig evolved from the 4-poster ("post" is a bit of a misnomer, as the 4 or 7 actuators are anything but inert posts). 4-posters were and still are used in the vehicle industry to simulate chassis vertical dynamics as the vehicle travels over a rough road, by generating forces at the tire contact patches using electro-hydraulic servo-actuators. They are also used to characterize the suspension by exciting the 4-wheel patches, with either sine-sweeps or randomly (white noise). When Formula 1 teams first used them in the 1980's, stimulated by the desire to understand active suspension systems, aerodynamic downforce was generated by attaching low-rate springs front and rear. These were generally bungees or tensator-type, constant-force springs. Downforce does not affect the vertical dynamics, other than to pre-load suspension springs, which may have non-linear characteristics and will certainly have load sensitive friction, i.e. damping. In the post-active era of the 1990's, as Formula 1 teams started to invest heavily in simulation and R&D facilities, they wished to simulate all the vertical forces experienced on the track, including aerodynamic loads that changed with attitude and load transfer loads due to inertia. Three additional actuators, of rather different specification to those under each wheel, apply these loads and they must do so in a way that does not affect the vertical dynamics of the car - Figs. 1 and 2.
 |
|
 |
The 4 main actuators (see Figs. 3, 4 and 5) are each capable of generating a force of 25KN, at a maximum velocity in excess of 1m/s. They are able to operate at up to 500Hz, but this performance is not necessary as the tires absorb any inputs in excess of around 50Hz. The hydraulic cylinders have hydrostatic bearings to withstand side loads without friction (there is no metal-to-metal contact between piston or rod and the cylinder) and the only seals are low-pressure seals on the rod to prevent seepage from the hydrostatic rod bearings. Hydraulic oil is fed from the 100KW power supply and main hydraulic accumulator to a smaller accumulator mounted on the actuator, and thence to twin Moog servo valves capable of flowing 63lpm. Another accumulator, also mounted on the actuator, damps exhaust pulsations. Position and load, measured just under the low-friction wheel pads, are fed back to the control system. Servo drive circuits amplify signals from the control system, measured in milliwatts, and the actuators are each capable of delivering around 500KW instantaneously.
The 3 aeroloader actuators present a different problem. Mechanically they are similar to the wheel actuators, though their load capacity is slightly less at 20KN. However, they must track the motion of the sprung mass of the car, even when it goes into resonance, without varying the applied load. Velocities may be as high as 3-4m/s, and this requires an additional servo valve stage. This high response valve, designed specifically by Servotest to maximize aerodynamic accuracy, has a first stage rated at 5lpm, driving a second stage spool valve rated at 250lpm. However, it is the load control strategies for the aeroloader actuators that provide the challenge. Because of the inevitable small lags in the control loops, they act as viscous dampers and affect the natural motion of the unsprung mass. Increasing the loop-gain leads to instability before it solves the problem. Additionally, the impedance (effective mass) of the car at the attachment point is included in the load control loop, and so any change in car set-up affects the response. There are a number of possible solutions and Servotest combines two of them. Mechanical compliance (a secret and sophisticated mechanical compliance element) is placed in series with the actuator, between it and the car attachment. It is not possible to make this compliance soft enough to completely solve the problem, as the rate of load changes during braking would be compromised, and so it is combined with velocity feed-forward. The control system measures or predicts the velocity of the attachment points and makes the actuator follow this motion. The combination of the two approaches succeeds in removing the impedance from the control loop and permits stable control of aero and inertia loads to between 20-50N, which is considered acceptable. Servotest's DCS2000 Digital Control System, with its PC operator interface and Race Car Test Software, controls the whole system.
 |
|
 |
Once a 7-post rig is installed - which is in itself not a minor task, as the actuators must be mounted on a seismic block of concrete, weighing hundreds of tonnes, to isolate the vibrations caused by running the system from nearby buildings - the R&D engineers can use it for a number of tests. Simplest are quasi-static suspension characteristics tests, yielding load/displacement curves for suspensions, roll control systems and allowing suspension kinematics to be measured with appropriate sensors. Resonance tests of the whole car on its suspension and tires are performed using sine sweeps and random excitation. The fact that the tire is not rotating introduces an inaccuracy, as the damping of a static tire is less than a rotating one. Servotest could replace the tires with four more actuators to simulate them, but to make it worth their while they would need to know precise rolling tire characteristics. They don't. Formula 1 teams are known to spend considerable time setting up the springing and damping of their cars for individual circuits, using their 7-post rigs. To accurately reproduce the track profile, the drive signals for the wheel actuators must be derived from measurements made on the track. Unfortunately, these cannot actually be directly measured on the track, and so wheel (push rod) load and displacement, and hub accelerations are measured instead and Servotest ICS software iterates the inputs to the actuators until the same responses are measured on the rig. The file is then frozen for that track. Aero maps are used for downforce variations with speed and attitude, and inertia loadings come directly from longitudinal and lateral g measurements on the track, all being applied via the three aeroloader actuators.
To expand the use of Servotest products in the motor sport industry to levels of racing that cannot justify the investment that a 7-post rig requires, Servotest offers the use of their in-house 7-poster, to anyone wishing to hire it. This provides a cost-effective way to assess and set-up a new design of racing car at the beginning of a season: a process that does not need full time access to the facility. Figure 6.
Precision servo-actuators, and the control and hydraulic power supply systems to go with them, are Servotest's core products. They are used by motor racing teams to test dampers (the emergence of electro- and magneto-rheological fluid damping systems, means that damper testing requires more than simple cyclic excitation), static and fatigue testing of structural components, resonance testing of assemblies and the whole car (the regular early season spate of rear wing failures is indicative of the need to understand the resonant characteristics of the rear end of the car) torsion testing of engine and transmission components, material testing, and load sensor calibration. Servotest manufactures a range of linear and rotary servo-actuators that can be tailored to the customer's requirements and combined into multi-axis test rigs. Rotary actuators come in three forms: vane types (either single vane, 270¡ stroke; or dual vane, 90¡ stroke); piston (20¡ stroke, but up to 500Hz band width); or swash plate hydraulic motors, which have continuous rotation. The latter are used for steering systems and gearboxes.
 |
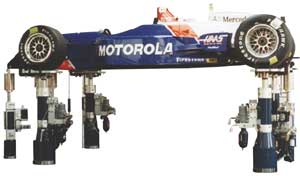 |
Fig 6 - 1997 Reynard chassis, owned and raced by PacWest Racing Group in the CART series, mounted on Servotest 7-post rig. (PacWest now operates a Servotest 7-post rig at their Auto Research Cener in Indianapolis) |
© Servotest Ltd. |
|
 |
Servotest has identified a potential requirement for full-power/full-speed testing of racing transmissions, to enable not only durability to be developed, but also gear change and differential control strategies. Providing 800+PS to power a Formula 1 transmission at full torque and speed, would be a formidable task, although engine/transmission combinations are run on engine dynamometers. Instead Servotest propose a rig in which two swash plate motors provide input power to the transmission, and two swash plate pumps absorb the power at the half-shafts. By clever plumbing and control, the power absorbed is used to drive the rig, and only sufficient power to overcome transmission losses, hydraulic losses and inertia effects has to be supplied by an external source. The system can be reversed to simulate overrun conditions, and so up and down gear changes can be faithfully simulated. Differential control of the output pumps simulates cornering effects and allows differential performance and control to be assessed. With limited winter testing on the agenda for the future, developing transmissions (the Achilles heel of the modern Formula 1 car, and the cause of more lost points early in the season than any other component) must either be brought forward well into the previous season, or undertaken in the laboratory. It cannot be long before Formula 1 teams are queuing up for transmission test rigs.
Motor racing is a demanding and high profile part of Servotest's business, but its customer list of companies outside motor sport contains many well-known names in the automotive, automotive components, materials test, earthquake simulation, transportation, man-rated simulation, and aerospace industries and research establishments. Servotest has formed partnerships with Burke E Porter in the USA, Lotus Engineering in the UK, Zetatek in India, Servo2000 in Germany and Italy, Figes in Turkey, and Berendsen in France, to ensure it is represented world wide and customers receive the support they require.
If it needs moving or shaking, Servotest can probably provide the equipment to do it.